If you work in the food manufacturing or food safety industry, you’ll know how important it is to handle complaints and non-compliances properly.
With risks of food-borne illness and injury, it’s imperative that preventative and corrective actions are taken immediately.
However, it can be a challenge trying to manage feedback and resolve issues from major customers, consumers and distribution partners while adhering to strict food safety quality control processes.
Luckily, there are ways to effectively manage these challenges - all you need is the right technology.
Integrated Software In Place Of Spreadsheets
If you are trying to manage your complaints, incidents and risk via a spreadsheet, you are going to run into some problems.
With no centralised workflow, no birds eye view, difficult reporting structure and non-standardised processes, it’s likely that key information and underlying issues will be missed.
Having cloud-based, industry-specific, integrated software managing your complaints and compliances will quickly improve how you respond and resolve the enquiries you receive…
Particularly if it has functions specifically made for the food manufacturing and safety industry.
Quality Alerts
The food industry is all about quality - no one is going to buy the goods you provide if they aren’t enjoyable or edible.
With a solution like Complaints Pro®, quality alerts are built into the software which automatically detect complaints related to the same product batch within a specific time horizon. This is achieved by detecting patterns of complaints with the same characteristics in real time.
As a result, you can be alerted if anything is amiss with the products you are distributing.
Shelf Life Assessment Module
Another function of quality assurance software like Complaints Pro® is the shelf life assessment module.
This provides the process for managing sampling, testing and logging, ensuring your products are conforming to your specified expiry dates.
It also captures individual shelf life assessment scores with averages of individual scores summarised.
With an industry-specific software, you can guarantee freshness to your clients without fail.
Root Cause Analysis
Getting to the bottom of what is causing the complaints you receive is essential in effectively resolving them.
With Complaints Pro®, our root cause analysis function uses our built-in Ishikawa (fishbone) diagrams with the ability to download or email the diagram directly from the software.
If there are systemic issues within your company, or a particular workflow is not functioning as it should, our system will analyse the complaints and breaches you receive and effectively alert you to the cause.
How Complaints Pro® Can Help
At Causia®, we’ve created the Complaints Pro® Food Safety Industry pack with your business and clients in mind.
Our software has all of the aforementioned features and more built-in to help you to provide the best possible service and improve your business with ease.
Some additional features include:
- Reason Code Hierarchies
- Investigation Requests
- Refund Management
- Death, Serious Illness or Injury Alerts
- Complaints Per Million Reporting
- Website Integration
With every feature you could possibly require built in, our cost-effective, centralised workflow provides the best practice management of complaints and non-compliances.
Talk to our team of complaints experts and book a demo of our Complaints Pro® software today.
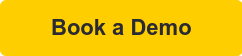